"Materials
Management with SAP S4HANA Business Processes and Configuration" by
Jawad Akhtar and Martin Murray
Introduction
Manage your materials with SAP S4HANA! Whether your
focus is on materials planning, procurement, or inventory, this
guide will teach you how to configure and manage Materials Management
with SAP S4HANA: Business Processes and Configuration.
Start by creating your organizational structure
and defining business partners and material master data. Then, follow
step-by-step instructions for essential processes, from purchasing
and MRP runs to goods issue and receipt. Discover how to maximize
SAP S4HANA capabilities with batch management, demand-driven
MRP, SAP Fiori reports, and built-in tools.
1. Configuring Materials Management with SAP S4HANA
Organizational Structure Setup
-
Define Company Code, Plant, Storage Location, and Purchasing
Organization.
Material Master Configuration
-
Create and configure material types with number ranges
and field selections.
-
Define industry sectors and material groups for material
categorization.
-
Set up units of measure and validate configurable objects.
Business Partners in SAP S4HANA
-
Set up vendors and customers with integrated business
partner functionality.
2. Procurement and Planning in SAP S4HANA
-
Purchasing information records and vendor-specific pricing.
-
Special procurement types such as subcontracting,
consignment, and external services.
-
Requests for quotations (RFQs) and purchase orders (POs).
-
Material Requirements Planning (MRP) and forecasting
for optimal stock management.
3. Inventory Management in SAP S4HANA
-
Goods Issue (GI) and Goods Receipt (GR) for material
movements.
-
Physical inventory processes for stock verification.
-
Invoice verification and material valuation using
Material Ledger.
4. Advanced Processes in Materials Management
Enhance your SAP S4HANA capabilities with:
-
Batch management for tracking
and quality control.
-
Demand-driven replenishment (DDMRP)
to optimize stock levels.
-
Document Management System (DMS) for handling material-related
documentation.
-
SAP Fiori apps for real-time reporting and system
monitoring.
5. Key Features and Functionalities
This guide covers all critical aspects of Materials Management
with SAP S4HANA, including:
-
Material master data management and its role in business
operations.
-
Business partner setup and integration for procurement
efficiency.
-
Purchasing and procurement processes, including purchase
requisitions, RFQs, and special procurement types.
-
Batch management for tracking materials and ensuring compliance.
-
Material Requirements Planning (MRP) and Demand-Driven
MRP (DDMRP).
-
Goods Issue (GI) and Goods Receipt (GR) processes for
accurate stock movement tracking.
-
Material Ledger functionality for inventory valuation
and invoice verification.
-
Advanced reporting tools, including SAP Fiori apps,
for better materials management insights.
6. SAP Fiori Reporting & Analytics for Materials Management
SAP S4HANA introduces powerful SAP Fiori applications
to improve decision-making. Key benefits include:
-
Real-time procurement and inventory insights.
-
Automated reports for tracking stock movements.
-
User-friendly dashboards for material planning and monitoring.
7. Key Differences: SAP ERP vs. SAP S4HANA for Materials Management
Feature |
SAP ERP |
SAP S4HANA |
Database |
Traditional relational DB |
In-memory HANA database |
Processing Speed |
Batch-based processing |
Real-time processing |
User Interface |
SAP GUI |
SAP Fiori with modern UX |
MRP Capabilities |
Classic MRP |
Demand-Driven MRP (DDMRP) |
Inventory Valuation |
Manual updates |
Real-time Material Ledger |
About the Author
Jawad Akhtar is an SAP logistics and supply chain
management expert specializing in business sales and delivery.
He earned his chemical engineering degree from Missouri University
of Science and Technology, USA.
With over 20 years of professional experience,
including 16+ years working with SAP systems, he has participated
in multiple large-scale, end-to-end SAP implementation projects.
Jawad helps SAP clients identify and resolve business challenges using
SAP solutions and change management strategies.
His expertise covers next-generation SAP products,
including:
✔ SAP S4HANA
✔ SAP Integrated Business Planning (SAP IBP)
✔ SAP Ariba
✔ SAP Customer Experience
Martin Murray was a respected logistics consultant
and worked with IBM for more than 15 years.
He joined the computer industry upon his graduation from
Middlesex University in 1986. In 1991, he began working with SAP
R/2 in the materials management area for a London-based multinational
beverage company.
In 1994, he moved to the United States to work as an SAP
R/3 consultant.
FAQs
1. What is Materials Management with SAP S4HANA?
It is an SAP module that manages procurement, inventory,
and material planning efficiently.
2. How does SAP S4HANA improve procurement processes?
With SAP Fiori apps, real-time analytics, and Demand-Driven
MRP, businesses can optimize purchasing and reduce procurement lead
times.
3. What is the role of MRP in SAP S4HANA?
MRP helps businesses plan and manage materials by
automating stock replenishment and ensuring optimal inventory levels.
4. What are the benefits of using SAP Fiori for Materials
Management?
SAP Fiori offers intuitive dashboards, real-time data access,
and user-friendly navigation, improving decision-making and operational
efficiency.
5. How does batch management enhance materials tracking?
Batch management enables lot-wise tracking of materials,
ensuring quality control and traceability in production and inventory management.
6. What are the key differences between SAP ERP and SAP S4HANA
for Materials Management?
SAP S4HANA features a simplified data model, real-time analytics,
and seamless integration with SAP cloud solutions, unlike traditional SAP
ERP.
Summary
Materials Management with SAP S4HANA: Business Processes
and Configuration is a comprehensive guide designed to help organizations
configure, manage, and optimize procurement, inventory management, and
material planning. |
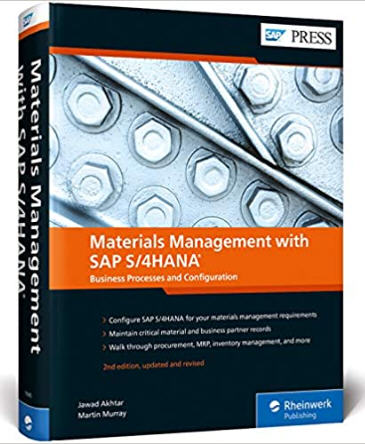 |
|
SAP Books
|